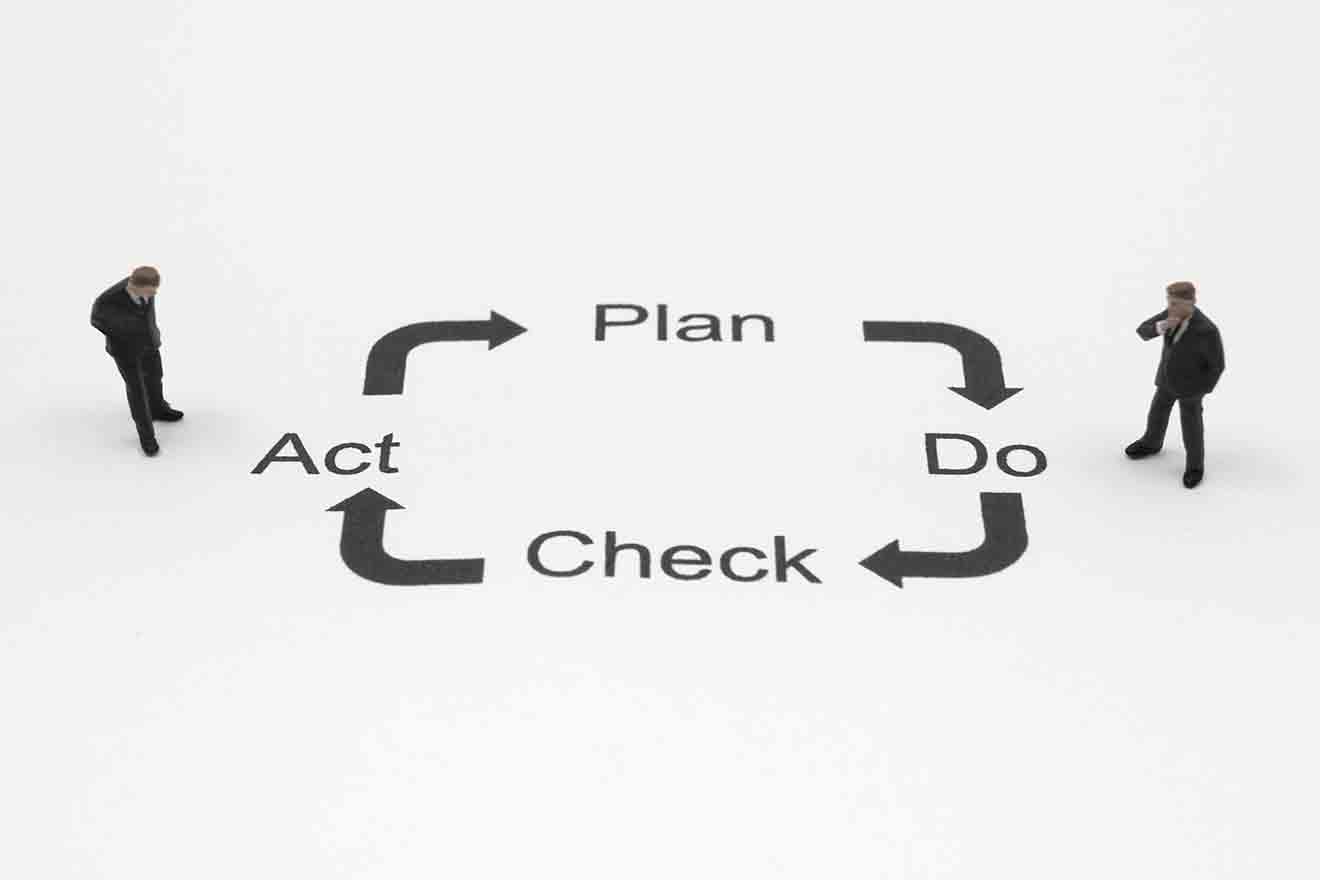
継続的な業務効率の改善、向上を目指すフレームワーク「PDCAサイクル」は、業界や業種を問わずビジネスのさまざまなシーンで活用されています。
本記事では、PDCAサイクルの特徴や、導入するメリット・デメリットのほか、PDCAサイクルをバックアップするデータの取り扱いなどについて詳しく解説します。
目次
- PDCAサイクルとは
- 1. Plan(計画)
- 2. Do(実行)
- 3. Check(評価)
- 4. Action(改善)
- PDCAサイクルを導入するメリット
- 継続的に業務を改善できる
- 目標や課題が明確になる
- 組織全体でスキルアップできる
- PDCAサイクルを導入するデメリット
- 形骸化するおそれがある
- サイクルが完了するまで時間がかかる
- 新しいアイデアが生まれにくい
- PDCAサイクルを実施した企業からみる具体例
- トヨタ自動車の例
- 無印良品の例
- PDCAサイクルの各プロセスにおける失敗要因
- Plan(計画)の失敗要因
- Do(実行)の失敗要因
- Check(評価)の失敗要因
- Action(改善)の失敗要因
- PDCAサイクルを成功させるためのERPの必要性
- 新しいフレーム枠「OODA(ウーダ)」とは
- PDCAサイクルとの違い
- まとめ
- よくある質問
PDCAサイクルとは
PDCAサイクルとは、「Plan(計画)」「Do(実行)」「Check(評価)」「Action(改善)」の頭文字をとったマネジメントサイクルを指すビジネス用語です。
P→D→C→Aのプロセスを繰り返しながら、継続的な業務効率の改善、向上を目指すフレームワークとして、業界や業種を問わずビジネスのさまざまなシーンで活用されています。

Plan(計画)・Do(実行)・Check(評価)・Action(改善)それぞれの段階について、詳しく解説していきます。
1. Plan(計画)
「Plan(計画)」では、現状ある問題や課題をしっかりと分析し、これらを解決する定量的な目標を設定します。定量的とは「物事を数値化できるさま」という意味です。
目標は「売上10%増加」といった数値や数量で表すことができる要素を設定するのがよいでしょう。逆に「社員のモチベーション向上」など数値で表せないものはPDCAサイクルには不向きです。
また、課題や現状の問題点を分析する段階には、PDCAサイクル以外のフレームワークも積極的に使用することで小さな問題を可視化し、共有するようにしておきましょう。
- 目標は定量的な数値を掲げる
- 実行の期限を決める
- 目標を達成するための実施行動や優先事項など検討し計画する
2. Do(実行)
計画ができたら、次は「Do(実行)」です。「Plan(計画)」で立てた計画に基づき、具体的な役割を実行していきます。
実行する中でプロセスや結果、問題点は、うまくいった事項だけでなく、手こずったこと、できなかったこと、実行する中で新たに生まれた課題などについても記録しておきましょう。目標と現状の差異を把握したり、次のプロセス「Check(評価)」で役立ちます。
- プロセスや結果、問題点について記録しておく
- 可能な限り数値的な結果が得られるように設定する
3. Check(評価)
計画通りに実行できたか、目標達成に結びついたかといった振り返りを通して、確認・評価を行うのが「Check(評価)」のプロセスです。
この時、できた・できなかっただけでなく、このサイクルで得た結果の要因を洗い出したり、計画自体に無理がなかったか?といった確認をしておくことで気付きの精度がアップします。考察の際には、以下のポイントに挙げた視点も参考にしてみてください。
- 計画通りに実行できたか
- なぜ、その結果になったのか
- どんな成果があったか
4. Action(改善)
「Action(改善)」では、ここまでのプロセスで得た課題に対して具体的な改善策を考えます。高い精度で改善案を設定できると、次のサイクルの質が格段に上がります。
複数の改善案が生まれた場合には、優先順位を明確にした上で、共有しておきましょう。
- うまくいった部分を考察し次回の計画に活かす
- うまくいかなかった点は改善案を検討する
- 改善案に優先順位をつける
- 改善の見込みがない場合、中止や延期も考慮に入れる
改善案が整ったら、再度「Paln(計画)」から次のPDCAサイクルをまわしていきます。繰り返すごとに課題が解決する手応えを実感できるようになるでしょう。
PDCAサイクルを導入するメリット
PDCAサイクルを導入するメリットを以下にピックアップしました。ここからは、PDCAサイクルを導入するメリットをひとつずつ解説していきます。
- 継続的に業務を改善できる
- 目標や課題が明確になる
- 組織全体でスキルアップできる
継続的に業務を改善できる
PDCAサイクルは基本的に中長期的な改善を前提としており、P→D→C→Aのプロセスで終わりではなく、P→D→C→A→P→D……と繰り返しながら、連続してフィードバックを重ねていきます。よって、継続的に業務をブラッシュアップし続けることができるという点が大きなメリットとして挙げられます
さらに、常に現場スタッフがタスクを更新するためスタッフのモチベーションアップにも効果的です。
目標や課題が明確になる
数値化された具体的な目標の立案、クリアすべき項目の優先順位が明確となるPDCAサイクルでは、スタッフ個人が目標達成のために何をすべきかがはっきりと分かります。
このため、PDCAサイクルを導入することで業務効率化がすすみ、個々の仕事に専念できる環境づくりに役立つという側面もあります。
組織全体でスキルアップできる
PDCAサイクルでは組織全体で学習を重ね、改善ノウハウを蓄積しながら知識を共有できるため、チーム全体の目標達成能力が底上げされます。
また、現場スタッフそれぞれがPDCAサイクルを回すという経験を重ねるため、優先順位のつけ方やフィードバックのスキル、目標を高解像度で理解する能力などが向上し、人材育成にもつながるでしょう。
PDCAサイクルを導入するデメリット
PDCAサイクルがビジネスのさまざまなシーンで活用されているとはいえ、当然ながらデメリットとなる側面も存在します。ここからは、PDCAサイクルのデメリットを見ていきましょう。
- 形骸化するおそれがある
- サイクルが完了するまで時間がかかる
- 新しいアイデアが生まれにくい
形骸化するおそれがある
本来の目的を見失い、とりあえず計画して行動するだけ、またはPDCAサイクルを回すことが目的となっているなど、PDCAサイクルが形だけのものになってしまうケースです。
改善の意図を理解しないまま、形式としてPDCAサイクルを回しても効果的な改善を果たすことはできませんし、サイクルさえ回しておけばよいという雰囲気になっては本末転倒です。
また、サイクルを回すことに労力をかけすぎて他の業務を圧迫してしまわないよう注意しましょう。
サイクルが完了するまで時間がかかる
PDCAはサイクルの構造上、「実行」から次の「実行」までの間に「評価」「改善」「計画」というプロセスを経る必要があります。このため、実行に時間がかかり、スピードに弱いというのが大きなデメリットとなります。
スピードが重視される業界や業種の場合、PDCAサイクルでは賄いきれないことが想定できるので、他のフレームワークも検討してみることをおすすめします。
新しいアイデアが生まれにくい
前例や過去のデータを元に計画し、改善を継続するPDCAサイクルは、視点を変えた打開策を講じたり新規事業を生み出すことに向いていません。
新しいアイデアやイノベーションを創出するには、後述するフレームワーク「OODA」が得意とするところです。詳しくは本記事「新しいフレーム枠「OODA(ウーダ)」とは」をご覧ください。
PDCAサイクルを実施した企業からみる具体例
PDCAサイクルの導入を検討または運用の見直しをする際、参考になるPDCAサイクル成功事例を2つ紹介します。
トヨタ自動車の例
成功事例として広く知られる「トヨタ生産方式」は、「3M(ムリ、ムダ、ムラ)」を排除してコストダウンし、徹底的に効率的な生産を目的としたPDCAサイクルです。
トヨタのPDCAサイクルにおいて特筆すべき点は、「5W1H」の手法を取り入れていることです。
一般的に「5W1H」は、「When(いつ)」→「Where(どこで)」→「Who(誰が)」→「What(何を)」→「Why(なぜ)」→「How(どのように)」を基本構成とする思考整理のフレームワークです。
トヨタの「5W1H」は、「Why(なぜ)」を5回繰り返したのち「How(どのように)」を導き出します。
これにより、「なぜ課題となっているのか」「なぜうまくいったのか」といった具体的かつ深い分析がスムーズにおこなわれるようになり、課題やタスクの改善策を立体的にします。
「Why(なぜ)」の追求が特に役立つのは、PDCAサイクルの「Plan(計画)」「Check(評価)」のプロセスです。
トヨタのPDCAサイクルのプロセス
・Plan(計画)
「トヨタ生産方式」を採用して「ムリ・ムダ・ムラ」を排除します。生産効率を高め、車の製造にかかる時間を最短にするシステムを構築しました。
・Do(実行)
必要なときに、必要な量だけ、停滞なく生産する「ジャストインタイム」体制を導入しました。異常が発生した時には機械が自動停止し、不良品の製造をストップする「自働化」を採用しています。
・Check(評価)
不良品の発生や問題の兆しが見えた時点で、支援を要請する権限を持つ現場作業員と管理者がともに問題の検証を行います。
・Action(改善)
技術者、管理者、ライン労働者が協力する「改善提案」の実施、できることはすぐ採用という企業文化の醸成の他、カスタマーサポートに注力しています。
さらに、トヨタのPDCAサイクルでは「Action(改善)」の後ろに「F(Follow)」が加わります。
・F(Follow)
メンバー全員がPDCAサイクルの目的に関心を持ち続ける、複数の人員でPDCAサイクルについて議論するといった「F(Follow)」を追加しています。その結果、PDCAサイクルを回しながらも精度を上げ続けることを可能にし、トヨタは現在のグローバル企業としての地位を築きました。
無印良品の例
業績が低迷した2001年、トップダウンでの指示により、紙の提案書は廃止、社内での提案はA4用紙1枚に収めるようにというルールが設定されました。
通常、PDCAサイクルは「Plan(計画)」からスタートしますが、良品計画のPDCAサイクルが特徴的だったのは「Do(実行)」からスタートしたことです。
これは、それまで「Plan(計画)」に費やしていた膨大な時間を「Do(実行)」に回すことで、組織全体の実行力を高める結果となりました。
この後の業績は見事なV字回復を果たしました。Do重視の方針とPDCAサイクルの仕組み化という組み合わせで、成功をおさめた好例として知られています。
良品計画のPDCAサイクルのプロセス
・Plan(計画)
planは余裕がある時に行い、まずは目の前の重要事項に着手します。
・Do(実行)
膨大な時間をDoに費やし、実行力が強い組織の体制を構築しました。
・Check(評価)
社内マニュアルは3カ月ごとに更新などのルールを設定しました。
・Action(改善)
週に1度、「Check(評価)」と「Action(改善)」の場を設けるといったルールで、PDCAサイクルを形骸化させない仕組み化に成功しています。
PDCAサイクルの各プロセスにおける失敗要因
多くの企業やプロジェクトで採用されているPDCAサイクルですが、使い方を誤ると思うような結果がでないことも想定されます。ここでは、PDCAサイクルのプロセスごとに陥りがちな失敗要因を紹介していきます。
Plan(計画)の失敗要因
「Plan(計画)」のプロセスで考えられる失敗要因として代表的なものは、目標値が高すぎて計画が現実的ではない計画を掲げてしまうことです。
これは仮説の段階で現状分析の精度が低いことに起因し、この後の「Do(実行)」「Check(評価)」でも満足のいくアクションを実行することが難しくなってしまいます。
十分な結果を得られない場合、スタッフのモチベーションも上がらず、負のスパイラルに陥ってしまいます。仮説の段階からしっかりと現状を分析し、具体的にイメージできるプランニングを行いましょう。
Do(実行)の失敗要因
「Do(実行)」の段階でよく見られる失敗は、計画性のないプランにより実行ができなかったというものです。
実施スケジュールや計画内容が詳細に決められていない場合は、タスクの具体的なアクションがわかりにくくなり、現実的ではない計画では実行することすらできないといった残念な結果に終わります。
また、実行中の記録が不十分だと「Check(評価)」もあいまいになるため、記録用のフォーマットを準備するなどの策も有効です。
Check(評価)の失敗要因
「もう少し頑張ろう」「概ね合格点だろう」といった曖昧な評価では、PDCAサイクルを効果的に活用することができません。
主観が混ざった評価基準では、実際に効果が得られていないのに評価してしまうというようなことも起こり得ます。
事実に基づいた評価が業務改善につながると理解し、具体的で数値的・定量的な目標による客観的な評価を心がけましょう。
Action(改善)の失敗要因
「Action(改善)」のプロセスでの失敗要因は、改善の視点の偏りです。
改善の素点が少ないと、適切な改善策を立案できませんから、「顧客からはどう見えるか」「取引先からはどう評価されるか」など、多方面からの視点を模索しましょう。
また、改善策が整ってもアクションが着実でなければ、PDCAサイクルの効果を発揮することができません。改善がうまくいかない場合は、課題そのものや目標の本質を見直すなど、繰り返し設定を行う必要があります。
PDCAサイクルを成功させるためのERPの必要性
PDCAサイクルを成功させるためには、経営に関わる資源の管理方法も重要となります。そこで提案したいのが「ERP(企業資源計画)」です。
ERP(企業資源計画)とは、Enterprise Resource Planningの略で、企業経営の資源である「会計」「人事」「生産」「物流」「販売」などの機能を統合して一元管理し、業務や企業全体の効率化を実現するためのシステムです。
ERPを採用することは、データ管理やチーム内での情報共有が容易となり、PDCAサイクルの失敗リスク低減にも繋がります。
ERPについて詳しく知りたい方は、別記事「ERP(企業資源計画)とは?導入メリットやERPの種類をわかりやすく解説」をご覧ください。
新しいフレーム枠「OODA(ウーダ)」とは
新しいアイデアやイノベーションを創出するとして先述した「OODA(ウーダ)」は、意思決定のためのフレームワークです。
OODA(ウーダ)とは、「Observe(観察)」「Orient(方向づけ)」「Decide(判断)」「Action(行動)」の頭文字を取った言葉です。
計画や評価、振り返りといった思考に時間をかけるポイントがないため、迅速な行動にもフレキシブルに対応可能で、競合の動きや顧客ニーズに柔軟な対応が求められるビジネスシーンで有用であると注目されています。
観察〜行動というほぼ全てのプロセスを現場担当者が担うので、各スタッフが自分の行動に責任を持ち、主体的に取り組みやすくなるなどもメリットとして挙げられます。
PDCAサイクルとの違い
PDCAサイクルは中長期的な視点で堅実に計画を立てて実行していくので、継続的な業務改善・向上を目指す際に有効なフレームワークです。
一方、OODAは最初に目標を設定せず、短期的な視点で現場の状況に応じて迅速な意思決定に向いているため、外部環境の変化が激しい業種・業界のほか、臨機応変な対応が求められるシーンや急なトラブルへの対応などにも活用されています。
同時に、業務の品質向上や改善といった根気強く取り組みたい継続的な課題にはフィットしないフレームワークです。
行動の前に計画を練るPDCAサイクルと、現状に応じすぐに行動するOODA、それぞれの特性と状況に合わせ使い分けることでスマートな経営を行いましょう。
まとめ
多数あるフレームワークの中でも「PDCAサイクル」は、多くのビジネスパーソンに認知され、さまざまなシーンで活用されています。とはいえ万能のものではありませんから、その特性をよく知り「ERP(企業資源計画)」などを活用しながら経営に活かしていきましょう。
また、解決したい課題に応じて「OODA」などほかのフレームワークを検討するなども有用です。
よくある質問
PDCAサイクルとは?
PDCAサイクルとは、「Plan(計画)」「Do(実行)」「Check(評価)」「Action(改善)」の頭文字をとったマネジメントサイクルを指すビジネス用語です。P→D→C→Aのプロセスを繰り返しながら、継続的な業務効率の改善、向上を目指すフレームワークとして、業界や業種を問わずビジネスのさまざまなシーンで活用されています。
詳しくは記事内「PDCAサイクルとは」をご覧ください。
PDCAサイクルを実施するメリットは?
主なメリットとして「継続的に業務を改善できる」「目標や課題が明確になる」「組織全体でスキルアップできる」などが挙げられます。
また、うまく活用することで、スタッフのモチベーションアップや人材育成、働きやすい環境の醸成にも効果を発揮します。
詳しくは記事内「PDCAサイクルを実施するメリット」をご覧ください。